Plywood is a construction material made from different species of trees.
It consists of thin wood layers or piles known as veneers bonded with an adhesive. With the used of resin, veneers are glued together with the adjacent layers causing each of its wood grain to be rotated up to a maximum angle of 90 degrees. The purpose of this is to improve the strength of the finished product and to reduce shrinkage.
There are two kinds of plywood: the hardwood plywood and the softwood plywood.In manufacturing plywood, the commonly used hardwoods are those fall in with the deciduous species such as larch, maple, oak, cherry, and poplar. Harwood plywood is categorized under plywood Standard Industrial Classification (SIC) Code 2435, and North America Industrial Classification System (NAICS) Code 321211 for ‘’Hardwood and Veneer’’. These Hardwood plywood are usually used in designing inner part of houses. The best example of these interior applications is for cabinets, furniture, store fixtures, doors, paneling, flooring, and architectural millwork,birch plywood near me.
On the other hand, softwood falls in with the family of coniferous. Firs and pines are softwoods used in manufacturing plywood. By bonding several layers of dry softwood veneers together with a resin, softwood plywood is being made. Softwood plywoods are categorized under SIC Code 2436, and North America Industrial Classification System (NAICS) Code 321212, for ‘’Softwood Plywood and Veneer’’. The apa plywood most common application of softwood plywood is those in construction. It is used as construction materials such as roof decking, sheathing, wall sliding, floors, concrete form boards, and containers.
Manufacturing hardwood or softwood plywood undergo different processes to ensure the quality of the product produced. These methods include selecting the log, debarking, cutting the logs, peeling the log, making a continuous ribbon of wood, cutting and stacking, gluing the wood, pressing the wood, trimming, sanding, and finishing used plywood.
1. Selecting the log
The initial step in manufacturing plywood is selecting the logs. Logs are chosen according to its physical properties. Maturity, straightness, and roundness are the most critical factors to be considered in selecting raw logs. Plywood manufacturers also ensure that all raw logs used in plywood come from a legal source and sustainable forest concession,best plywood for outdoor use.
Submerging logs in water over a period helps to peel and cut down logs into various sizes easily. Some other mills, especially in cold places use heat as a way to improve the quality of peeling. These methods are known as hydrothermal processing wickes 18mm ply. Request a Quote
2.Debarking
The second step is the debarking process. Logs are feed into a debarking machine. Just like shown in the picture. As the logs rotate from the ridged wheels, the cutting head on the track is reversely rotating with the log from end to end, causing the bark to be removed. The purpose of this is to peel the bark without damaging the wood,ace hardware plywood.
3.Cutting the logs
After the debarking process, the logs are cut into desired lengths in step known as bucking. This process is done so that the next operation which is peeling the bark can be efficiently executed 12mm birch plywood
4.Peeling the logs
The next step is the peeling process. The markings in the log made by the debarking knives during the debarking process are removed using a substantial rotary lathe. The log revolves on the machine against a long blade cutter. The cutting process is like sharpening a pencil except that the blade is parallel with the log at the time of cutting wholesale plywood prices. Request a Quote
5.Making a continuous ribbon of wood
After peeling, the next method to be done is creating a continuous ribbon of wood. The log rotates and feeds towards the cutting edge of the lathe creating continuous and unwounded thin layers of wood. The thickness of the veneer depends upon how it is used 4×8 pressure treated plywood.
6.Cutting and stacking
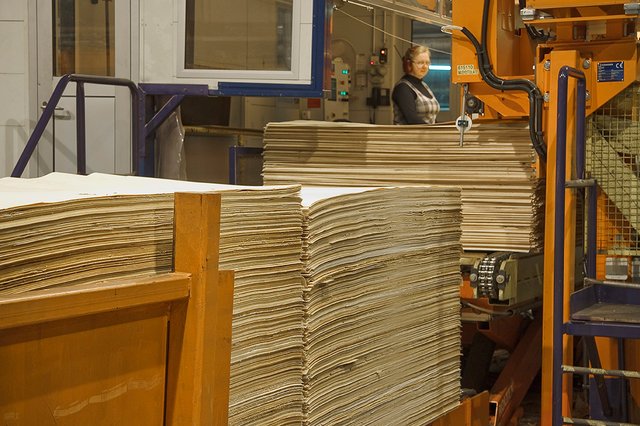
The piece of wood is cut to a standard size of 4’ x 8’plywood. The ideal thickness of plywood range from 1/4” to 3¼’, but the actual thickness of the plywood after production is determined after the sheets are pressed and glued together. The sheets are automatically scanned as it comes up in the peeler. After scanning, it is stack in preparation for transferring and drying using drying ovens sanded plywood home depot.
7.Gluing the wood
After cutting and stacking, the next step is sticking the sheets of veneer together. This is done to determine the desired thickness of the plywood sheets. The commonly used adhesive in manufacturing plywood are those synthetic plastics such as phenol – formaldehyde or urea resins. The thin sheets of wood run through the gluing machine. As the sheet pass through, the glue is spread evenly on the back and face of the veneer. The glued veneer is placed on top of unglued veneer, then followed by glued veneer. The process is alternating: glued, unglued, glued, unglued and so on 7mm plywood. Request a Quote
8.Cold Pressing the board
After doing he glued and unglued alternating process, the sheets which are glued together is pressed using a hot press machine to attain the desired thickness of plywood. An example of this pressing machine is the hydraulic or pneumatic pressing machine wherein pressure, or sometimes heat and pressure are applied to the plies. When heat is applied, the glue hardens quickly and then solidifies as the combined veneer is pressed together. The plywood is considered dry once the pressure is released burnt plywood flooring.
9.Hot Pressing (Daylight Press)
This part of the production process is where the actual panels begin to take shape. Multiple panels are loaded into the daylight press. The Daylight Press then compresses and maintains heated pressure on the boards for a long period of time. This creates and maintains required contact between the glue and veneers. It also decreases tension in the glue line and the thickness of glue layer gurjan plywood price.
10.Trimming, Sanding, and Finishing
The sheet will undergo processes to make it presentable and saleable in the market. These methods include trimming, sanding, and finishing. Because of these processes, the sheets takes down into standard sizes which meet the needs of the customers. Also, these processes are the reason why plywood seen in the market has smooth edges and texture. Each finished plywood products have the desired quality grade based on the requirement of U.S Commercial Standard CS – (35 – 36) (Wood 468). These quality grades are indicated by letters A to C which A is the highest, and C is the lowest. The finished plywood products are divided into two categories indicating whether it is for exterior or interior used wood sheet price.
11.Quality Control
The final product has to be assessed for quality but it wouldn’t be very efficient just to wait until the end of the process to find a large problem with production. For this reason, mills control their production by carrying out a number of tests on different sections of the production process e.g. testing moisture levels, formaldehyde release, durability, wickes ply etc.
Many mills have what is called a Factory Production Control certificate which means they have been audited by a third party and had their production process approved to relevant European standards.
12.Packaging
Finished products are then stacked up and banded together. Any relevant CE marks are printed on the packaging 18mm plywood b&q.
13.Delivery
We take delivery of plywood weekly, ready to despatch to you!exterior ply