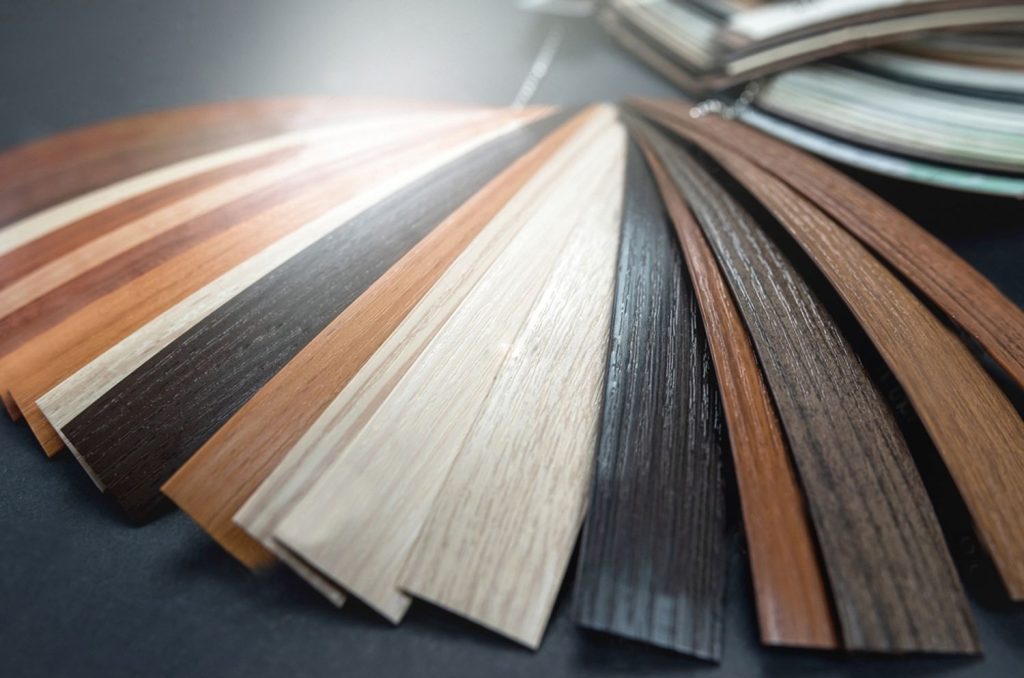
The amount of adhesive impregnated paper has a great influence on the surface properties of decorative MDF, such as water resistance, heat resistance, wear resistance, finish, smoothness and chemical pollution resistance. In this paper, we will study through experiments to understand the changes in the surface properties of decorative MDF when the amount of adhesive impregnated paper changes under the same production process.
Wood-based panel is a composite plate processed by wood or non-wood plant materials. It is widely used in modern building decoration due to its advantages of being economical and lightweight. With the development of wood-based panel construction technology, the product structure of wood-based panels is becoming more and more rich. At present, there are three main types of wood-based panels: fiberboard, particleboard and plywood, which have their own characteristics in terms of construction technology and plate performance. Impregnating film paper is the decorative paper of wood-based panels, which is used to decorate the surface of wood-based panels and protect the wood-based panels. The quality of wood-based panels is closely related to the quality of impregnating film paper. The adhesive amount of construction technology seriously affects the protective effect of impregnating film paper on the plate, and finally determines the comprehensive performance of waterproof, heat resistance, finish, smoothness and other properties of the surface of decorative MDF. Therefore, the research on the adhesive amount of impregnating film paper is of great significance for the quality of wood-based panels, and is the basis for ensuring the innovation of wood-based panel products.
Overview of impregnated film paper
Impregnated film paper refers to decorative paper soaked with phenolic resin or melamine resin. After drying, the impregnated film paper can be covered to the surface of the wood-based panel by hot pressing construction technology, which is used to decorate the wood-based panel, and also has the role of protecting the wood-based panel. After soaking the impregnated film paper absorbs the volatile substances in the resin, the surface becomes smooth and smooth, and its heat resistance, water resistance, wear resistance and other properties are also improved, which can greatly improve the application performance of artificial sheet. In the construction of impregnated film paper, the range of impregnated glue should be controlled between 120% and 170%. So when the amount of impregnated film paper is between 120% and 170%, what kind of changes will be made in the surface properties of the veneer MDF?
Experimental research
(1) Test materials
Prepare plain base paper with a quantity of 75g/m2; Medium density fiberboard; Urea-formaldehyde resin and melamine formaldehyde resin. The size of MDF is 2440mm×1220mm×15mm, the moisture content is 5.7%, the density is 0.71g/cm3, the solid content of urea-formaldehyde resin is 47.85%, the pH value is 7.6, and the viscosity is 14.31s (coated 4 cups, 25℃). The solid content of the melamine formaldehyde resin is 52.3%, the pH value is 9.7, and the viscosity is 15.91s (coated 4 cups at 25℃).
(2) Test method
According to the relevant provisions of GB/T28995-2012, the traditional variable analysis method was applied to test the influence of the change of the UF glue amount in the range of 120%~170% on the surface properties of MDF by changing the UF glue amount in a single dipping test. The influence of the construction technology on the surface properties of MDF was tested by adjusting the ratio of glue content while keeping the same amount of glue. The production process of impregnated film paper is shown in Figure 2 below, and the impregnation test process refers to the production process of impregnated film paper. In the test process, the five levels of 103%, 122%, 143%, 163% and 181% from the range of 40% to 170% were used to detect the influence of the change of glue content on the surface performance of the finished MDF.
Three sheets of impregnated film paper were used to veneer the MDF. The construction process was a single veneer hot pressing technology. The construction parameters were 50° smooth surface of the hot pressing steel plate, 30 seconds hot pressing time of the veneer, 190℃ temperature, and 14MPa hot pressing pressure. The performance index of the finished MDF after hot pressing veneer molding can be tested only when it is placed horizontally in the room for more than 48 hours.
(3) Performance testing
According to GB/T15102-2006 “impregnated film paper veneered wood-based board”, the veneered MDF must be cut to the specified size, and the test items are divided into water vapor resistance, crack resistance, dew bottom resistance, cold and hot cycle resistance, heat resistance, pollution and corrosion resistance, etc.
The test results are as follows: in the case of the same construction technology, when the amount of glue is 103%, the performance indicators of the three pieces of decorated MDF are only qualified for cracking resistance, one of them is qualified for pollution resistance and corrosion resistance, one is qualified for water vapor resistance, and the rest are unqualified, and the final result is judged as unqualified quality of decorated MDF. When the amount of glue is 122% and 143%, the performance indicators of the three veneered MDF are all qualified, and there is no dew bottom, which indicates that the overall performance indicators are excellent. When the glue content is 163%, most of the performance indicators of the three veneer MDF are qualified, and one of the performance indicators of the veneer MDF is not qualified, which indicates that the performance indicators are good and need to be improved. When the glue content is 181%, the performance indicators of the three veneer MDF show a number of unqualified, among which the cold cycle resistance, crack resistance, pollution corrosion toxicity resistance and water vapor resistance show that the three board indicators are all unqualified, and the wear resistance index is good, and the final determination is that the quality of the veneer MDF is qualified, and it is classified as the lowest grade of the veneer MDF. The above surface performance quality test results show that the impregnated film paper with the glue content of 122% and 143% has the best surface performance when applied to the veneer of MDF, followed by 163%, 181%, and 103% has the worst performance. This reflects from the side that under the same impregnation construction process, when the impregnation amount is in the range of 120%-160%, the surface properties of the veneer MDF are better, the impregnation content is gradually reduced from 120%, and the comprehensive performance is gradually reduced, and the impregnation content is gradually increased from 160%, and the comprehensive performance is gradually reduced. Among them, the lower amount of glue affects the surface wear resistance, heat resistance, pollution corrosion resistance and water vapor resistance of the finished MDF surface, while the higher amount of glue affects the surface crack resistance, pollution corrosion resistance, water vapor resistance and cold and hot cycle resistance of the finished MDF surface. Based on the performance test results of this test, it is suggested that the construction parameters of impregnated film paper should be controlled within 120%-160%.
According to the above test process, in the process of producing impregnated film paper, when the amount of secondary impregnation glue is always maintained at 60%, the total amount of impregnated glue is between 120% and 140%, the surface performance index of the finished MDF is the best.
Conclusion: In summary, in the production of impregnated film paper, the construction process of the amount of impregnated glue not only has a greater impact on the surface energy of the veneer MDF, but also affects the production cost. It is recommended that the construction adjustment of multiple dipping amount should be adopted before production, and the dipping amount should be controlled between 120% and 150%. This construction parameter is helpful to reduce the construction cost and optimize the performance of the finished MDF surface.