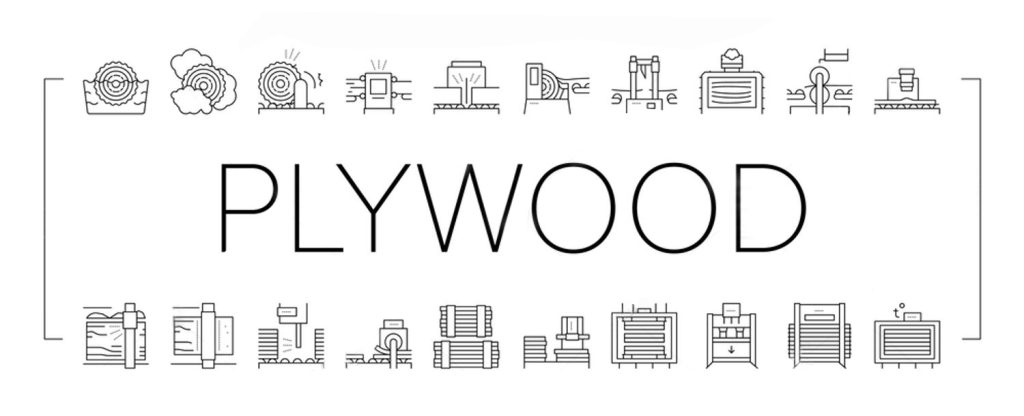
Scientific management of plywood production technology can effectively improve the overall quality of products and help enterprises achieve higher revenue. The content of plywood production technology management is extremely complex, covering a variety of management points. The in-depth discussion of different technical types involved has a significant positive effect on the following production work. Therefore, this paper discusses the impact of plywood production technology on product quality for reference.
Plywood production technology is a complex technology, which is because this technology in the actual production stage must deal with many different links, if you can not fully grasp the operation of a large number of key points, it may bring serious negative impact on the overall quality of the product. In the process of discussing the production status of the product, it can be found that many enterprises in the use of plywood production technology in the process of not achieving high quality management, so the final quality of production has also declined. Therefore, enterprises still need to grasp the key points of the management work in production, so as to achieve the improvement of product quality.
Ⅰ. Function and Application Area of Plywood
Plywood is one of the more common furniture materials in interior decoration. It is made by turning wood into veneers or cutting wood into thin sheets, and then gluing them together with adhesives. Its shape is mostly plate. Plywood is not only widely used in interior decoration. It also plays an important role in packaging, transportation and other aspects. There are a wide range of categories of plywood, which are usually classified by the differences between their uses.
Ⅱ. Measures to Improve the Technical Level of Plywood Production
In the process of plywood quality management, one of the most critical links is how to improve the current process management quality, to grasp the production of various links, to ensure that the quality of the product can always be in a relatively good state.In the process of plywood production technology research, researchers need to optimize the current production technology comprehensively, so as to further improve it, which has a significant impact on the quality of the product.Therefore, enterprises need to pay full attention to the relevance between production technology and product quality, and on this basis to ensure that the growth of product quality can be achieved according to expectations. In addition, the manufacturing of plywood basically adopts veneer cutting technology, which needs to go through a lot of processes, such as log cooking, peeling and wooden section centering, which are one of the more important manufacturing links.In the process of the above links, technical workers should ensure that all the links of the process can be completed according to strict standards, and solve many problems that may occur, which is because all the links must be paid attention to, so as to optimize the overall quality of plywood production technology.
Finally, before plywood manufacturing, the material preparation should be done well. The quality of the material preparation is an important basis for determining the quality of the final product. Therefore, sufficient attention should be paid to this link in the plywood production process.
Ⅲ. The impact of plywood production technology on product quality
1.Turn-cut link of plywood production technology
The production of plywood needs to go through a lot of processes. Therefore, this paper first discusses the turning process, so as to analyze several problems that staff need to pay attention to when they are engaged in turning engineering. This is helpful to effectively solve the above problems when working, and on this basis to further improve product quality and prevent it from being negatively affected by various factors. In order to avoid the quality risks of plywood in the market process, staff need to adhere to strict standards when turning, so as to prevent substandard finished products from entering the subsequent production process, so as to fundamentally solve the quality problem. Usually, veneer turning needs to make the thickness of veneer balanced. The difference between the two sides and the middle three points in thickness must be kept within ± 0.5mm, and it should also ensure that the surface finish and the tensile strength of the strip meet the requirements. However, due to the influence of different factors, the passing rate of turning is usually kept between 70-85%. In order to further improve its passing rate, production personnel must provide higher attention to it in the process of plywood production, and discuss the factors that affect its passing rate, so as to ensure the stability of product quality.
2.Influence of installation of rotary cutter pressure gauge on product quality and yield rate
The installation of the tool is of great importance for the production of plywood. If the quality standard is not reached in the actual operation, it may lead to the insufficient flatness of the wood section, vibration, splitting and other quality problems, which will eventually lead to a significant decline in the yield rate of the wood and lead to mechanical accidents. In the most serious case, it may even lead to the inability to continue production, which leads to the production of products by many inconveniences and leads to serious waste of materials. The main factor causing this problem is that the relative installation of the pressure gauge and the rotary knife does not choose the appropriate clearance of the knife door. The practical results show that the clearance needs to be maintained between 0.95-0.98mm in the top-down projection, and between 0.38-0.45mm in the horizontal projection. In terms of the height of the blade and the spindle, the blade should be higher than the center of the spindle, but should be lower than the height of the center of the spindle, and maintained between 0-0.5mm. In addition, the adjustment of the front and back angles of the tool should also be paid attention to. If the front angle exceeds the appropriate range, it may vibrate during the cutting. The diameter of the wood section is constantly reduced during the cutting, and the radial force is also reduced. If the limit requirements of the wood cutting can not be met, it is difficult to carry out normal cutting, and eventually lead to a large waste of raw materials. If the range of the front angle is too low, there will be problems of different thicknesses in the veneer cutting stage, which may not only lead to the clogging of the knife door, but also lead to splitting and other problems, resulting in serious threats to the life safety of the operator. In order to deal with this problem, a more suitable angle should be adopted to avoid the above problems. The choice of angle should be determined according to the specific conditions of the wood section and the production facilities. Usually, the main ones are: for the diameter of 300-600mm, the right angle should be kept between 2.5-3.0 degrees, and for the diameter of no more than 300mm, the back angle should be kept between 1.5-2.5 degrees. Its main principle is: the relatively large diameter of the wood section can be kept with the larger radial force, but it can not avoid the friction between the back angle and the wood section. Therefore, the angle of the back angle needs to be increased; while the relatively small diameter of the wood section is different, because the radial force it needs to bear will gradually decrease due to the cutting section, so the friction between the back angle and the wood section will also decrease, which may lead to the problem of knife jumping, so it needs to be lowered to ensure that the cutting can be completed. Usually, the adjustment of the equipment itself and the process demand can not effectively meet the needs of the operator. The best way is to ignore the value reflected by the rear angle of the equipment and check the friction width between the wood segment and the rotary knife, which can usually be maintained between 4-6mm.
3.The drying process of plywood production technology
According to the commonly used plywood production technology in the past, after the completion of the veneer drying process, it is necessary to ensure that its moisture content is maintained at about 8-12% before it can be glued into hot pressing board. However, when the moisture content of the thin veneer is maintained at 8-12% for drying treatment, it may also lead to deformation and warping of the thin veneer, and ultimately lead to a more serious negative effect on the quality of the plywood. To solve this problem, it is necessary to adopt suitable dewatering adhesive to treat it and ensure that it can meet the technical requirements. Secondly, increase the moisture content of the thin veneer after drying treatment (usually 14-16%). Once again, the veneer made by various types of tree species should be distinguished, and then the glue formation should be carried out among various tree species according to the regulations; Finally, to further increase the pre-pressure and extend the pre-pressing time (usually need to increase the unit pressure to 1.OMPa, and increase the pressing time to 30 to 40min), reduce the hot pressing time, so as to meet the needs of dehydrating adhesive on the water content of thin veneer. Under normal circumstances, the use of dehydrating adhesives will also bring higher costs to the production process of the product, but because the water content of the thin veneer, the increase of pre-pressure and the reduction of hot pressing time, its energy consumption is also reduced, which makes the plywood board rate and product quality have been significantly improved, thus achieving economic growth.
The impact between plywood production technology management and product quality has been significantly reflected in most of the links, and this phenomenon also means that relevant workers should pay more attention to the quality of plywood production technology management. This paper first discusses the specific concept of plywood, and then analyzes how to improve plywood production technology and its impact on the final quality of products. It is hoped that with the continuous deepening of research, the final technology and product quality can be effectively developed.